Success story
Jumbo Supermarkets
Every day, Jumbo has an average of 800 trucks on the roads for distribution purposes. They needed better insight into the execution of transport activities and wanted to improve communication with carriers and consumers alike. They chose the Simacan Control Tower as the solution.
- Second largest supermarket chain in the Netherlands;
- 700+ Supermarkets in the Netherlands and Belgium;
- Second largest online supermarket in the Netherlands;
- Deliveries from 3 EFCs; 6 DCs; 18 hubs and 19 home delivery service locations.
Optimised supply chain visibility with Simacan’s Control Tower
Alberdine van Velzen, Manager Supply Chain Planning at Jumbo, comments: “Once our truck drivers had left the distribution centre, we literally had no idea where they were. Therefore, we decided to invest in optimizing our planning and gaining maximum supply chain visibility. We use Simacan’s Control Tower to monitor all the trips and also for all the associated communication. Besides that, we use a central advanced planning & scheduling (APS) system from Quintiq. Between them, those two systems give us optimal support – from strategic planning all the way through to the actual trips.”
A single system for all the logistics challenges
The decision was preceded by a thorough selection process. First of all, Jumbo conducted internal analysis to gain a clear picture of the needs. The retailer then drew up a document outlining its vision and invited several potential suppliers to present their ideas and products. Van Velzen: “We were looking for a single system to solve all our logistics challenges. Road freight is our primary transport activity, but home delivery has been growing rapidly too since we launched it in 2016. Simacan’s Control Tower immediately stood out for several reasons.”
Text continues below the photo.
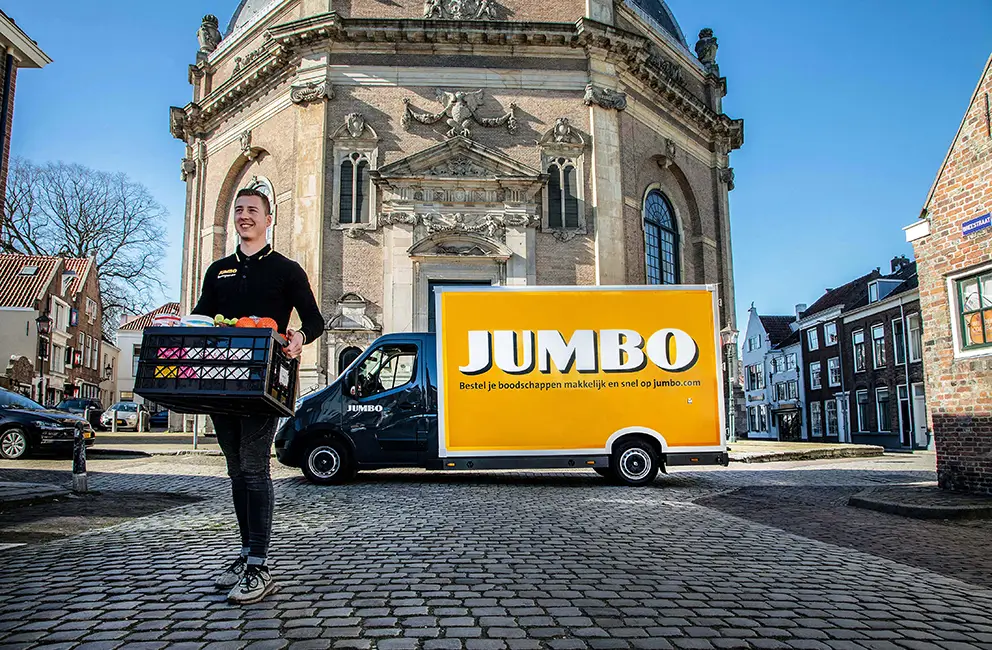
The power of the Control Tower
“Firstly, the platform calculates not only where a truck or van is right now, but also where it will be in three or four hours’ time. That’s the kind of information that helps us to optimize our efficiency. Besides that, we chose the Control Tower because it is already being used successfully within various organizations, both for road freight and for home delivery, including within organizations in our sector. That industry knowledge is an added bonus and is a seamless fit with our needs and with the situation here at Jumbo. We use around 40 different carriers for our store replenishment activities. Some are bigger than others, and they don’t all have the same degree of automation or the same transport management system (TMS). Even so, they can all connect to the Control Tower. We offer them a choice of ‘packages’; carriers can start with a very basic package, such as via an app for example. Or they can take it a step further by integrating their on-board computers, or even the complete TMS.”
Step-by-step approach
It was a conscious decision for Jumbo to gain experience with the platform on a small scale first: within home delivery, which is done using Jumbo’s own vans. Moreover, there was a clear need to improve the service level in that area by sending consumers automated messages about the expected delivery times. Jumbo accelerated the implementation of the Control Tower for its home delivery activities in late 2017. However, the Quintiq APS system was not set up for regional deliveries from stores at that time, so Simacan developed an interim solution called Plan-to-Go, a simple route planner which is now replaced by the APS system.
Control Tower to enhance home delivery and store replenishment efficiency
By early 2020, Jumbo had four hubs and approximately 100 stores working with the Control Tower for home delivery and seven stores for store replenishment. Anno 2025, all stores and locations are connected to Simacan. Van Velzen: “This benefits not only consumers, but our employees too. Consumers receive relevant and accurate delivery information sooner than they used to. Staff in our Jumbo Service Center have got more insight into the delivery status, receive fewer calls asking what time deliveries will be arriving, and no longer need to send text messages to customers manually. Last but not least, store managers have greater insight into the delivery activities and better information as the basis for decision-making.”
Shared challenge: Simplifying decentralized operations
Simacan is aware of a challenge too: “Jumbo’s decentralized home delivery organization means that lots of different users utilize our product for just a short time. If just one department worked with the system every day, we could provide central training. But in Jumbo’s case there are a lot of users, among them hundreds of stores and store managers for whom it’s an additional task. So we want to make things as easy as possible for them.” Van Velzen agrees: “Yes, that’s one of the considerations – ensuring that the Control Tower gains broad acceptance as part of our day-to-day processes.”
Seamless integration for retail success
Future proof solution
The Simacan Control Tower is now fully implemented nationwide for home deliveries, playing a central role in Jumbo’s end-to-end supply chain. Since its initial deployment in 2019, the platform has become integral to optimizing logistics operations, with its roll-out to Jumbo’s stores having begun in early 2020. Reflecting on the current landscape, Van Velzen remarks: “Logistics networks are increasingly interconnected across the sector. Over time, a market standard based on proven success develops for the entire industry, and I continue to see significant opportunities with Simacan’s Control Tower.”
Request a free Simacan demo!
Discover the benefits of Simacan by using it. Request a free demo today!
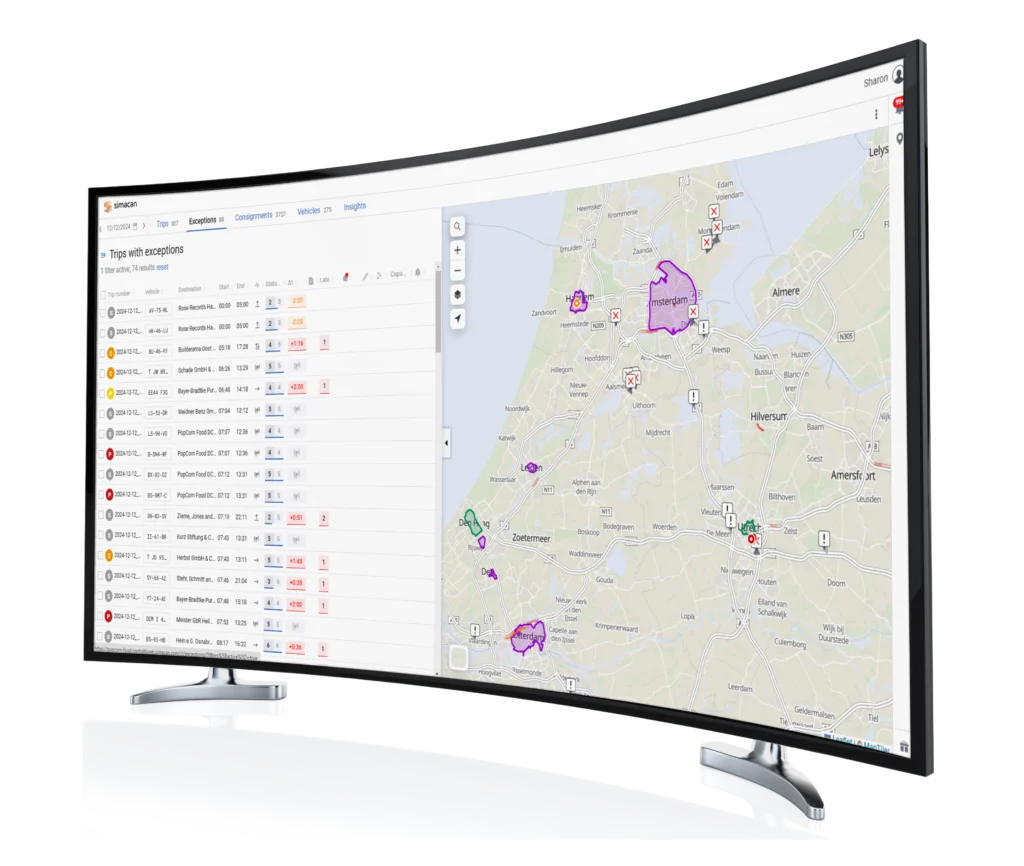