Success story
Bakery Borgesius
An optimal range of delicious fresh bread is available at opening time in all supermarkets – around 1,000 stores – supplied by the Borgesius bakery company. This is made possible by Borgesius’ extremely sophisticated transport operation to deliver the ordered bakery products every night/morning. Logistics Manager Leon den Boer explains how this daily task is managed, and the role that Simacan’s Control Tower plays. “The punctuality of deliveries has increased by 10% since we started using it.”
- Every day, Borgesius supplies approximately 800,000 bakery products to Dutch supermarkets from its nine bakeries;
- The company arranges the transport itself, from six regional locations throughout the Netherlands;
- Borgesius supplies approximately 1,000 stores daily;
- It uses a fleet of around 190 trucks.
Direct store deliveries
Few people have heard of this bakery company, despite its 125-year existence, but millions of people enjoy its fresh products every day. From wholewheat bread to white rolls, and from currant loaves to pastries – everything is produced to order the day before and delivered to the store at night or early in the morning. “We are one of the few suppliers who deliver directly to stores,” says Den Boer. “In fact, this is a huge operation every day. Bread is an emotional product that people go to the supermarket for especially. Our products must therefore be fresh on the shelves when a store opens.”
Complex logistics puzzle
Borgesius is a family business with nine production locations spread throughout the Netherlands. The daily trips to all store branches are centrally planned, but coordinated from six regional production locations. These are ultimately responsible for deliveries and returns/packaging collection in their region, and they either have their own means of transport or work with logistics service providers. Den Boer: “This is quite a complex puzzle. You have to deal with all kinds of restrictions, such as zero-emission zones and specific delivery conditions per store. We’re not allowed to deliver to some branches until an hour before opening, whereas we can deliver to others in the middle of the night. We do more trips on Fridays and Saturdays than during the week, and on Sundays we have to take different opening hours into account.”
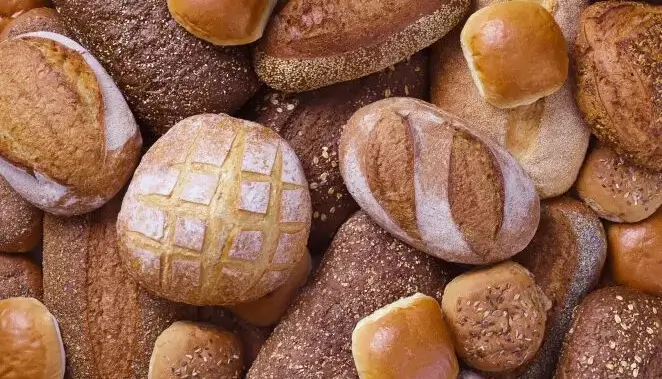
Punctuality and transparency
The three most important key performance indicators for Borgesius are punctuality, completeness, and transparency. “The most important thing, of course, is that we have delivered the bakery products as ordered to all store branches before opening time every day. We currently have a service level of 99.3% to 99.5%. We are also expected to accurately inform branches about our arrival time. We have been using Simacan’s Control Tower for that for a few years now. The big advantage of this is that store employees no longer have to call us in the morning to ask where their bread is. Thanks to the Simacan ‘arrival’ monitors, they can see that it is on its way. Our customers – the supermarkets – also use this solution for their own transport operations.”
Live track & trace for all stakeholders
Continuous improvement of transport process
Simacan facilitates visibility and communication during the trip. An additional advantage is that the stakeholders can also review how things went afterwards, as the basis for improvements. “The logistics managers at the production locations can monitor a logistics service provider’s performance and analyse why delays occur,” says Den Boer. “If a branch receives its delivery late, you want to know the reason why – especially if it happens frequently. For example, maybe the route is suboptimal and it would be better to plan branches in a different order. It is also possible that a driver loses a lot of time at a retail location if roll containers are in the way, for example. Whatever it is, everyone is looking at the same data, so there can be no arguments about that.”
"Everyone is looking at the same data, so there can be no arguments about that."
Borgesius Logistics Manager, Leon den Boer
Logistics KPIs are increasing
Better decisions thanks to data
Dynamic trip planning
Another potential idea is to make trip planning more dynamic – in other words, to calculate the most optimal trips on a daily basis rather than working with fixed schedules. Den Boer concludes: “This is one of the reasons why, after talking to our customers, we switched to Simacan. If that’s what you want, you need Simacan. We need to look more closely at how exactly this will look and whether we really want it. It certainly has advantages – you can respond better to changes in demand and make optimal use of transport capacity – but there are also disadvantages. If drivers get a different trip every day, that might affect job satisfaction and quality.”
Thanks to Simacan, Borgesius is able to deliver top-class performance every day, and the supermarket branches have real-time insight into the ETAs of their bakery orders. An additional advantage is that the company can continuously improve and make informed decisions about its future transport strategy.
Request a free Simacan demo!
Discover the benefits of Simacan by using it. Request a free demo today!
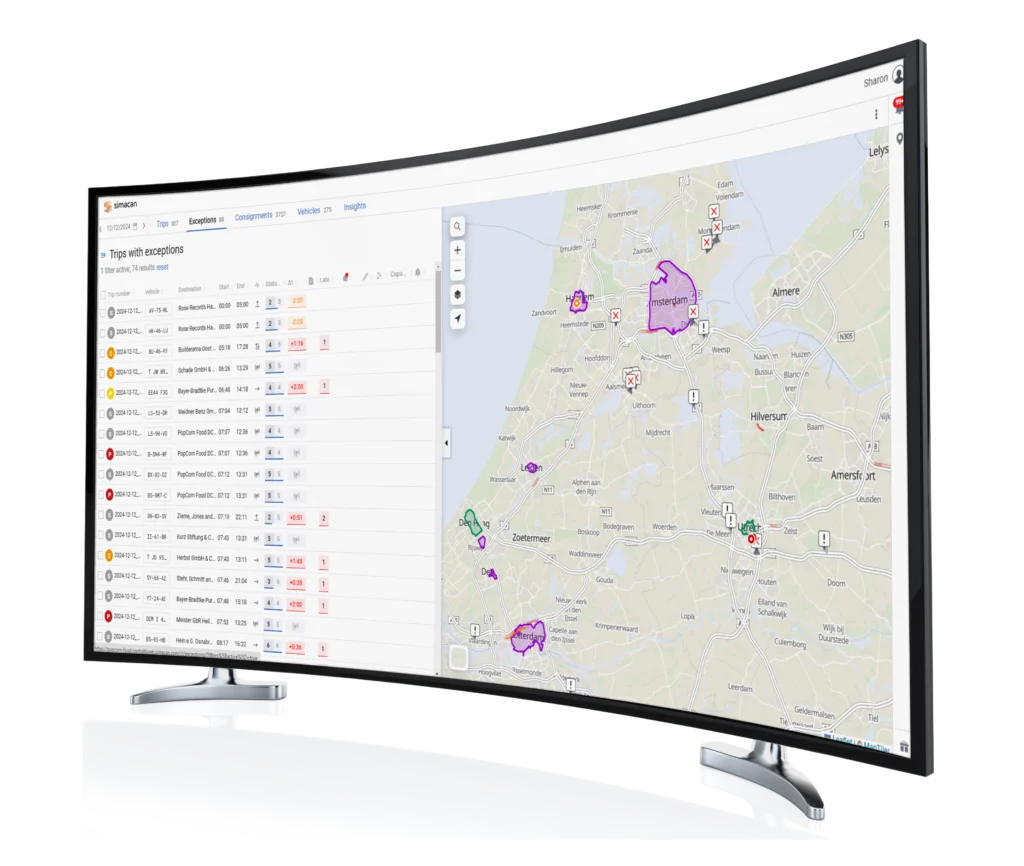