CONTENT
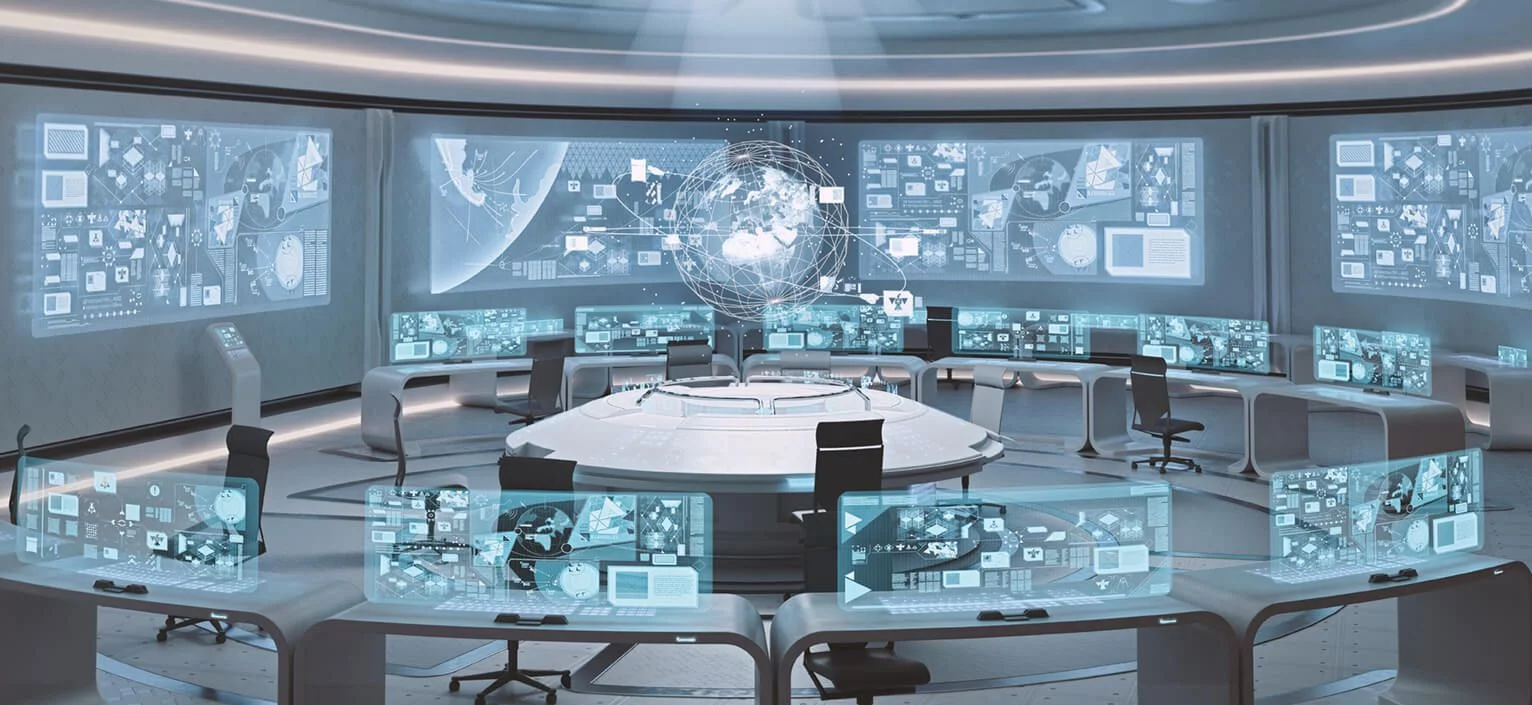
4C: Collaborating Control Towers for supply chain management
Command Center, Cross Chain Control Center or Cross Chain Collaboration Center (4C)… all terms for the same cloud-based collaboration solution. We will assume the term ‘Command Center’ for now. But what is a Command Center? How are they different from traditional logistics Control Towers? In this blog, we take a closer look at the differences in technology between a Command Center and a Control Tower.
Multiple logistics Control Towers working together
A Command Center… the quickest description – we think – is to think of it as a collection of multiple logistics Control Towers working together. With Command Centers, you are in control of complete logistic chains. In our Simacan Command Center, information flows of different logistic parties and chains are combined and exchanged. This bundling of data enables more effective handling and thus optimisation across chains. Chain partners can work together to set up chains more efficiently and sustainably. In this way, processes such as inbound logistics and regional distribution with the interplay of shippers and carriers can be linked. But also think of processes that are controlled separately but have a clear interface in connection. For example, linking energy and charge management to the transport management of electric vehicles.
The Simacan Command Center thus offers huge opportunities for improvement because it is precisely in the pivot points between different chains or processes that capacity is lost in practice. Two examples:
Example 1: Cross-docking
Suppose you manage a cross dock operation whose inbound and outbound transport flows are outsourced to different carriers. Naturally, these two transport operations need to be carefully planned and coordinated. But in practice things always go differently than planned. For example, a truck with incoming goods is delayed by an hour. In a cross-dock, this will have an immediate impact on the outgoing trips, but the problem is: nobody knows exactly which trips are involved and planners can only act to a limited extent. After all, the transporter of outbound flows has its own planning and different customers. The result is that empty miles are driven or planners reserve time buffers in the planning to avoid this. In short: waste!
Example 2: The last mile
Suppose you are a retailer and you have three different transport operations: from suppliers to distribution centre (DC), from DC to shops and from DC directly to consumer’s homes. Again, same question: what do you do if something goes wrong in the supply from supplier to DC that has consequences for the rest of the supply chain? The complexity of that question lies in the fact that you are dealing with multiple transport partners. Partners with their own interests and a span of control which is limited to their own operations. One cannot decide for others to adjust their planning. A retailer cannot force carriers to drive half-empty trucks for the same costs. The home delivery service provider cannot force network carriers to adjust their trips. In short, major efficiency losses result from these kinds of frictions between networks or links.
From reactive to proactive transport management
To cope with such ‘misfits’ between links, you would actually want to manage transport supply chains as a whole. This is where we enter the realm of logistics Control Towers. After all, these offer visibility over the entire chain and also the ability to intervene. The latter is important because whereas with a visibility system you can only intervene reactively, a Control Tower can act proactively. Control Towers can anticipate problems before they actually occur, making them a wonderful asset to the transport industry. They have already greatly benefited many transport organisations.
Transport is about working together
Yet in practice, the efficiency gains from Control Towers are still often limited to one domain. And that is precisely not the case in most transport operations. Even if you have control, that does not mean you can adjust a supply chain partner’s planning. A shipper cannot simply intervene in the logistics provider’s planning, just as that logistics provider has nothing to say about the parcel carrier’s last mile. They have no say over each other… but they can work together!
That’s where Command Centers come in. To show how this works, let’s go back to the examples:
Example 1 with a Command Center: Cross-docking
Suppose, in the cross-docking operation, both carriers have their own advanced planning system (APS) and Control Tower. As mentioned earlier, the trips run out of schedule because a delay occurs. What a Command Center does now is signal that something changes (vehicle X arrives later than planned at DC); it calculates what this means (vehicle Y cannot leave on time); and supports the planner by proposing a solution (vehicle Y gets a different cargo load, vehicle Z takes over X’s delayed cargo load). The Command Center feeds this solution back to the carriers’ Control Towers in real-time. Coordination can now take place between the Control Towers: agree with this suggestion or solve it differently? Upon agreement, the rescheduling actions are implemented.
Example 2 with a Command Center: The last mile
Retail replenishment operations are useally carried out by multiple carriers. Suppose twenty shops have to be supplied by four trucks in one day. A large traffic jam on the motorway causes delays in the supply towards the DC. This means one shop’s replenishment order cannot be delivered completely. The Command Center signals this and calculates that the shop can be delivered completely if it is included in a later trip. This information is automatically shared with the carrier in the traffic jam and with the planner of the carrier supplying the shops. All the chain parties involved check whether they think this proposal is a good idea. If they jointly agree, they can adopt the proposal in their own Control Tower.
Control Tower vs Command Center
Command Center technology is explicitly aimed at facilitating collaboration and can thus help prevent the current losses between networks or links. Logistics service providers in supply chains can use Command Centers to pool capabilities, share assets and increase efficiency.
Horizontal supply chain collaboration
In short, the key differentiators between a Control Tower and Command Center is the scope of functional capabilities they offer. Where a Control Tower is mostly vertical and domain specific, a Command Center is horizontal, cross-functional and cross-chain. With a Command Center, you have a digital representation of the physical supply chain; a digital supply chain twin. For example, the Simacan Command Center provides detailed simulation to predict supply chain dynamics. Thus, exceptions can be predicted and actions taken to mitigate the impact.
This might also interest you:
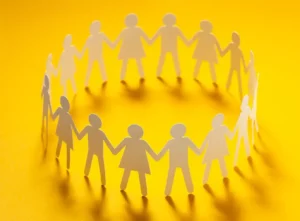
Orchestration in logistics: connecting what exists, steering what matters
Discover how transport orchestration enhances real-time logistics control by connecting systems, breaking down silos, and enabling smarter decisions. Learn how a logistics Control Tower adds
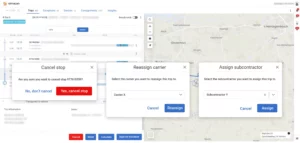
Transport Orchestration
Simacan’s Transport Orchestration is the central component of a modern transport management platform, providing seamless collaboration and secure data sharing within and across supply chains.