Beseitigen Sie Unsicherheiten in der Logistik!
Sichtbarkeit, Kontrolle und Zusammenarbeit in logistischen Prozessen
Simacan ist die Logistik-Control-Tower-Plattform für den Straßentransport und bietet Echtzeit-Transparenz, dynamische Routenoptimierung und nahtlose Zusammenarbeit. Jeden Tag ermöglichen wir Lieferketten in verschiedenen Sektoren, darunter Einzelhandel, B2C und Bau-Logistik, mit über 35 Millionen präzisen und effizienten Lieferungen pro Jahr.
Kernfunktionen
Die Funktionalität von Simacan ist in fünf leistungsstarke Module oder Funktionspakete unterteilt. Die ersten vier Module konzentrieren sich auf essentielle Transportprozesse: Planung und Vorbereitung, Kontrolle, Steuerung und Analyse. Das fünfte Modul, Transport-Orchestrierung, fungiert als verbindendes Element, das sicherstellt, dass diese Prozesse nahtlos ineinandergreifen und effizient zusammenarbeiten.
Transport Vorbereitung
Optimieren Sie die verfügbaren Planungsinformationen für vorhersehbare und effiziente Transportabläufe und eine optimale Ressourcennutzung.
Transport Kontrolle
Überwachen Sie Fahrzeuge, Tourverlauf und Lieferzeiten mit Echtzeit-Tracking-Technologie und aktuellen Verkehrsinformationen. Kommunizieren Sie proaktiv mit Kunden und Partnern, um eine bessere Zusammenarbeit und höhere Kundenzufriedenheit zu erreichen.
Transport
Analytik
Gewinnen Sie wertvolle Einblicke in die operative Leistungsfähigkeit durch umfassende Berichte. Nutzen Sie die Daten für Self-Billing, Emissionsberichte und datengetriebene Prozessoptimierung.
Transport Orchestrierung
Integrieren Sie Transportphasen nahtlos für effizientere Prozesse. Profitieren Sie von leistungsstarken APIs, benutzerfreundlichen Schnittstellen und Echtzeit-Datenverbindungen.
Hauptvorteile von Simacan
✅ Echtzeit-Transporteinblicke
Sofortige Sicht auf Transportstatus, Live-ETAs und Verkehrsinformationen für effiziente Entscheidungen und minimalen Zeitverlust.
✅ Verbesserte Effizienz
Optimieren Sie Ihre Lieferkette mit fortschrittlicher Planungssoftware, dynamischen Routenanpassungen und proaktivem Störungsmanagement.
✅ Nahtlose Zusammenarbeit aller Beteiligten
Verbinden Sie Systeme und Beteiligte mit leistungsstarken API-Integrationen und intuitiven Benutzeroberflächen für eine bessere Koordination.
✅ Zukunftssicherer Transport
Bereiten Sie sich auf emissionsfreie Zonen, neue Regularien und intelligente urbane Logistiklösungen vor.
✅ Automatisierte Kundenkommunikation
Informieren Sie Kunden und Partner automatisch über Planänderungen und Ankunftszeiten. Stärken Sie Zusammenarbeit und Vertrauen in Ihrer Lieferkette.
✅ Skalierbare globale Lösung
Simacan: Ihr verlässlicher Partner für Einzelhandel, Transportwesen und urbane Logistik
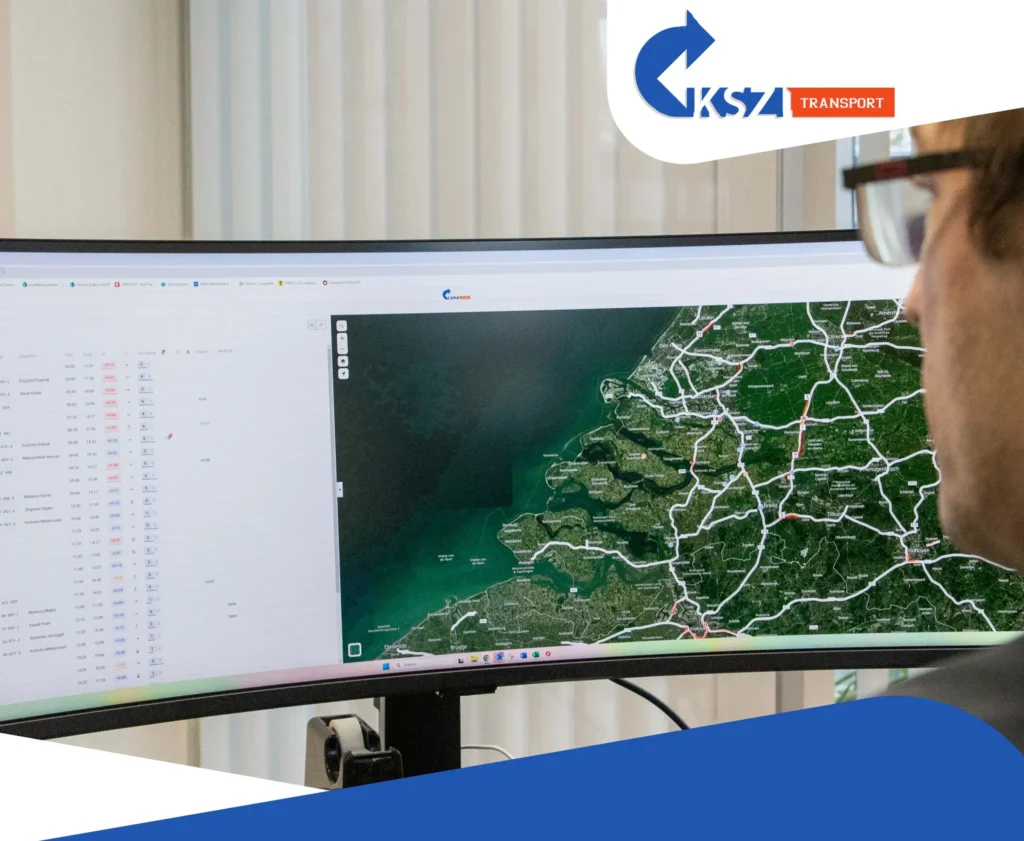
"Eine wichtige Verbesserung im Prozess ist die bidirektionale Integration zwischen dem internen Transport Management System (TMS) und der Simacan Control Tower. Diese Integration ermöglicht es Kunden, die Simacan nutzen, Fahrten direkt in das TMS einzugeben, was einen nahtlosen Informationsaustausch gewährleistet. Diese Effizienz erlaubt es uns, stets auf dem neuesten Stand zu bleiben und sofort auf Änderungen zu reagieren."
KSZ Transport, Betriebsleiter
Neueste Simacan Nachrichten
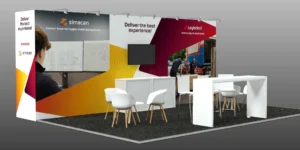
Simacan & Aventeon deliver the best experience!
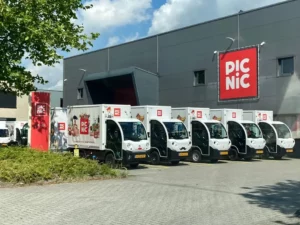
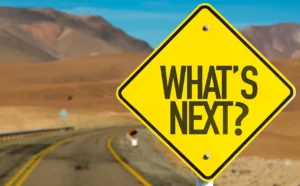
Die 5 wichtigsten Verkehrstrends für 2025
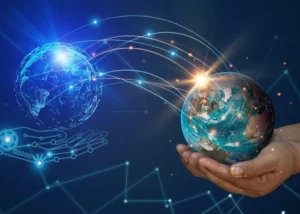